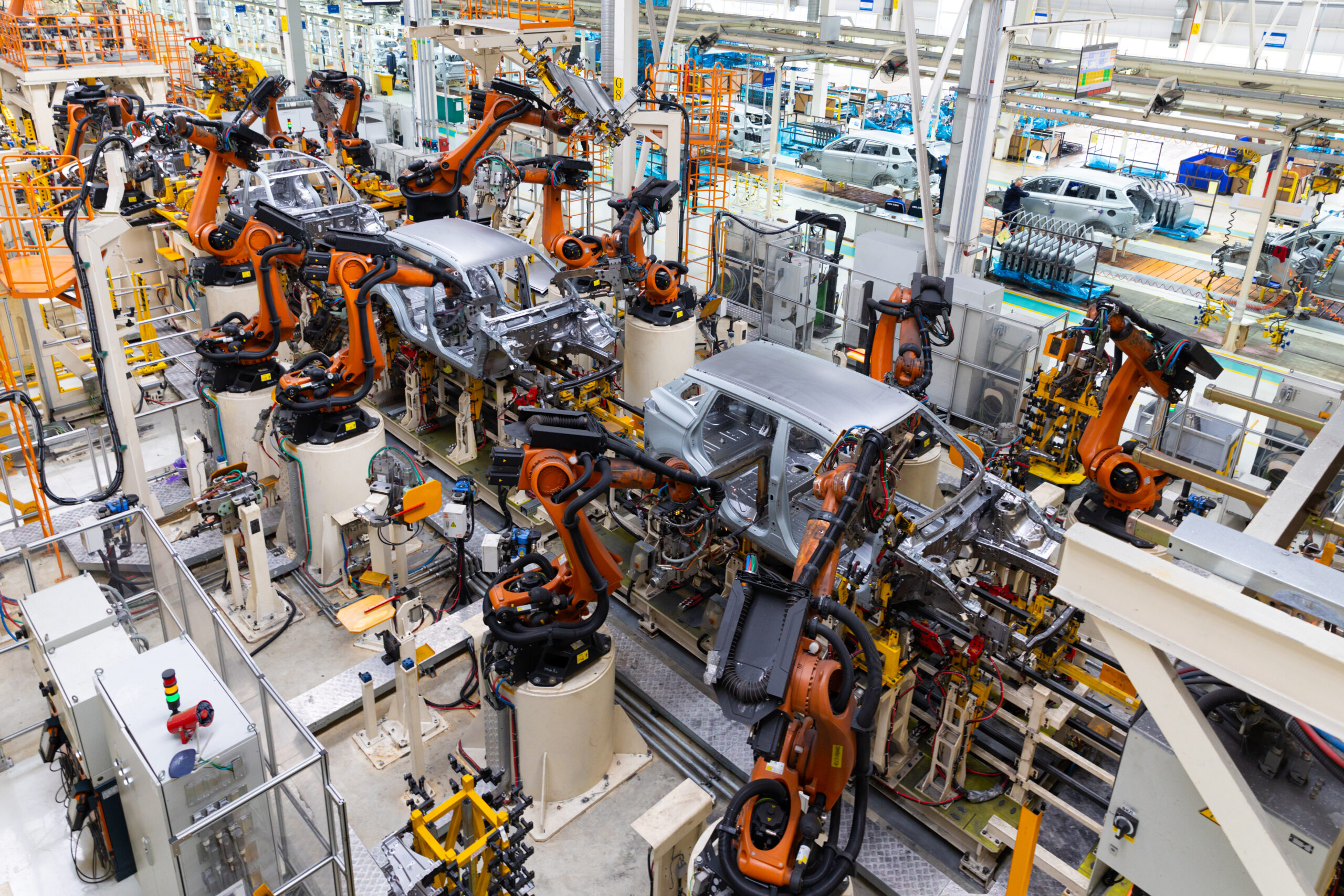
How Infor LN is Revolutionizing Manufacturing with Advanced ERP Features
The manufacturing industry stands at an unprecedented crossroads where traditional production methods intersect with revolutionary digital technologies. As global competition intensifies and customer expectations evolve at breakneck speed, manufacturing organizations must fundamentally reimagine their operational frameworks to remain competitive and profitable.
Infor is named a Leader in the 2024 Gartner® Magic Quadrant™ for Cloud ERP for Product-Centric Enterprises, positioning Infor LN as a critical catalyst in this transformation. This recognition underscores the platform’s ability to address the complex challenges facing modern manufacturers while providing the scalability and flexibility required for future growth.
Manufacturing enterprises worldwide are experiencing unprecedented pressures from multiple fronts. Supply chain disruptions have exposed vulnerabilities in traditional linear supply models, while environmental regulations demand sustainable production practices. Simultaneously, the rapid advancement of artificial intelligence, machine learning, and Internet of Things technologies presents unprecedented opportunities for operational optimization and competitive differentiation.
In this comprehensive analysis, we explore how Infor LN is not merely adapting to these changes but actively driving the transformation of manufacturing operations through its advanced ERP capabilities. From intelligent production planning to predictive maintenance analytics, Infor LN represents a paradigm shift from reactive operational management to proactive, data-driven manufacturing excellence.
The significance of this transformation cannot be overstated. The ERP market size in North America is worth over $20 billion in 2024 and is expected to reach nearly $32 billion by 2029, reflecting the critical importance organizations place on advanced ERP capabilities. However, the true measure of success lies not in market size but in the tangible operational improvements and competitive advantages these systems deliver.
The Manufacturing Revolution: Understanding the Digital Imperative
The Current State of Manufacturing
Modern manufacturing operates in an environment characterized by volatility, uncertainty, complexity, and ambiguity. Traditional manufacturing paradigms, built on predictable demand patterns and stable supply chains, are increasingly inadequate for navigating today’s dynamic marketplace. The COVID-19 pandemic accelerated many of these trends, forcing manufacturers to confront the limitations of their existing systems and processes.
From our research 67% of businesses stated that due to digital initiatives such as e-commerce, digital supply chains and remote working, they could continue to trade effectively during the pandemic. This statistic highlights the critical importance of digital transformation initiatives in maintaining business continuity and operational resilience.
The manufacturing landscape has evolved from mass production models focused on efficiency and cost reduction to mass customization paradigms that prioritize flexibility, responsiveness, and customer-centricity. This shift requires manufacturing systems that can accommodate frequent product variations, manage complex multi-tier supply networks, and provide real-time visibility across all operational dimensions.
Contemporary manufacturers face several critical challenges that traditional ERP systems struggle to address effectively. First, the increasing complexity of product portfolios demands sophisticated configuration management and engineering change control capabilities. Second, global supply chains require multi-currency, multi-language, and multi-regulatory compliance features. Third, sustainability initiatives necessitate comprehensive environmental impact tracking and reporting functionalities.
Technological Disruption and Opportunity
The convergence of multiple technological trends is creating unprecedented opportunities for manufacturing innovation. Artificial intelligence and machine learning algorithms can now process vast amounts of production data to identify optimization opportunities that human analysts might miss. Advanced sensors and IoT devices provide granular visibility into equipment performance and production processes, enabling predictive maintenance strategies that minimize downtime and maximize equipment effectiveness.
Cloud computing platforms offer scalability and flexibility that on-premise systems cannot match, while mobile technologies enable workforce mobility and real-time decision-making capabilities. Blockchain technology promises enhanced supply chain transparency and traceability, while augmented and virtual reality applications are transforming training, maintenance, and quality control processes.
However, realizing these benefits requires more than simply adopting new technologies. Manufacturing organizations must fundamentally rethink their operational processes, organizational structures, and performance metrics to leverage these capabilities effectively. This transformation demands ERP systems that can integrate seamlessly with emerging technologies while maintaining the reliability and performance standards that manufacturing operations require.
The Role of Advanced ERP in Manufacturing Transformation
Enterprise Resource Planning systems have evolved far beyond their original scope of inventory management and financial reporting. Modern ERP platforms like Infor LN function as comprehensive digital transformation enablers that integrate and orchestrate all aspects of manufacturing operations. They serve as the digital nervous system that connects production planning, supply chain management, quality control, and financial reporting into a cohesive operational framework.
The transformation from traditional ERP to advanced manufacturing platforms involves several critical dimensions. First, data architecture has evolved from transactional repositories to real-time analytical platforms that support predictive and prescriptive analytics. Second, user interfaces have transformed from complex, feature-rich screens to intuitive, role-based dashboards that prioritize actionable insights over data volume.
Third, integration capabilities have expanded from simple data exchanges to sophisticated workflow orchestration that spans multiple systems, partners, and geographies. Fourth, deployment models have shifted from monolithic on-premise installations to flexible, cloud-native architectures that support hybrid and multi-cloud strategies.
Ready to revolutionize your manufacturing operations with Infor LN?
Sama specializes in Infor LN implementation and optimization for manufacturing companies, helping you leverage advanced ERP features to streamline production, improve efficiency, and accelerate digital transformation in your manufacturing processes.
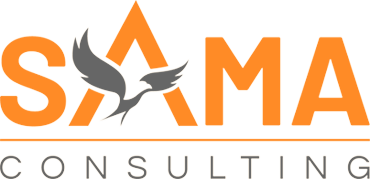
Infor LN: The Architectural Foundation of Modern Manufacturing
Technical Architecture and Design Philosophy
Infor LN represents a sophisticated evolution of ERP architecture specifically designed to address the complex requirements of discrete and process manufacturing environments. The platform’s technical foundation reflects decades of manufacturing domain expertise combined with modern software engineering principles and cloud-native design patterns.
The system architecture employs a multi-tier design that separates presentation, application logic, and data management layers to optimize performance, scalability, and maintainability. The presentation layer supports both traditional desktop clients and modern web browsers, enabling flexible deployment scenarios that accommodate diverse user preferences and device capabilities. Mobile applications extend this flexibility further, allowing critical manufacturing functions to be accessed from anywhere within the facility or across global operations.
The application logic layer incorporates sophisticated business rules engines that codify manufacturing best practices while providing the flexibility to accommodate industry-specific requirements and organizational preferences. These engines process complex manufacturing scenarios such as multi-level bill of materials explosions, capacity-constrained production scheduling, and advanced planning algorithms that consider multiple optimization criteria simultaneously.
The data management layer employs advanced database technologies that support both transactional processing and analytical workloads. Real-time data replication and synchronization capabilities ensure that all users have access to current information regardless of their location or the complexity of their queries. Advanced indexing and partitioning strategies optimize query performance even when processing millions of transactions and maintaining extensive historical data.
Scalability and Performance Characteristics
Manufacturing organizations require ERP systems that can accommodate significant variations in transaction volumes, user concurrency, and data processing requirements. Infor LN addresses these challenges through a scalable architecture that supports both vertical and horizontal scaling strategies.
Vertical scaling capabilities allow organizations to increase processing power and memory capacity on existing hardware platforms as their requirements grow. This approach provides a cost-effective upgrade path for organizations with stable user populations but increasing transaction volumes or analytical requirements.
Horizontal scaling capabilities enable organizations to distribute processing loads across multiple servers or cloud instances. This approach supports unlimited user growth and transaction volume expansion while maintaining consistent performance characteristics. Load balancing algorithms ensure that processing requests are distributed optimally across available resources, preventing bottlenecks and maintaining system responsiveness.
The platform’s caching strategies further enhance performance by storing frequently accessed data in high-speed memory systems. Intelligent cache management algorithms automatically identify and prioritize the most commonly used information while ensuring data consistency across all system components.
Multi-Site and Global Operations Support
Modern manufacturing organizations increasingly operate across multiple facilities, countries, and regulatory jurisdictions. Infor LN provides comprehensive multi-site capabilities that enable centralized management while accommodating local requirements and preferences.
The multi-company architecture supports complex organizational structures including holding companies, subsidiaries, joint ventures, and partnership arrangements. Each entity can maintain its own chart of accounts, currency, and reporting requirements while participating in consolidated planning and reporting processes.
Multi-currency capabilities extend beyond simple foreign exchange translation to support complex international transactions including letters of credit, forward contracts, and hedging strategies. Real-time currency conversion ensures accurate financial reporting while automated revaluation processes maintain compliance with international accounting standards.
Multi-language support encompasses both user interface translation and data content localization. Users can access the system in their preferred language while maintaining the ability to collaborate with colleagues who use different languages. Document management capabilities support multi-language templates and automated translation services for common business documents.
Ready to revolutionize your manufacturing operations with Infor LN?
Sama specializes in Infor LN implementation and optimization for manufacturing companies, helping you leverage advanced ERP features to streamline production, improve efficiency, and accelerate digital transformation in your manufacturing processes.
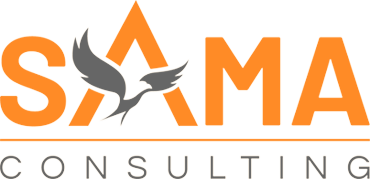
Core Manufacturing Capabilities: Beyond Traditional ERP
Advanced Production Planning and Scheduling
Infor LN’s production planning capabilities represent a significant advancement over traditional MRP systems. The platform incorporates sophisticated algorithms that consider multiple constraints simultaneously, including material availability, capacity limitations, tooling requirements, and skill set availability. This holistic approach to production planning ensures that schedules are both feasible and optimized for key performance indicators such as on-time delivery, inventory turnover, and resource utilization.
The Master Production Scheduling module employs advanced forecasting algorithms that analyze historical demand patterns, seasonality trends, and external market indicators to generate accurate demand predictions. These forecasts consider multiple variables including promotional activities, new product introductions, and market expansion initiatives. Machine learning algorithms continuously improve forecast accuracy by analyzing prediction errors and adjusting model parameters accordingly.
Capacity planning capabilities extend beyond traditional work center analysis to consider skilled labor availability, tooling requirements, and setup time optimization. The system can automatically reschedule production activities to accommodate equipment maintenance, operator training, and other planned interruptions while minimizing impact on customer commitments.
Advanced scheduling algorithms support both forward and backward scheduling methodologies, enabling planners to optimize schedules based on material availability or customer delivery requirements. The system can automatically identify critical path activities and suggest alternative routing or resource allocation strategies when constraints threaten delivery performance.
Material Requirements Planning Excellence
The Material Requirements Planning functionality in Infor LN incorporates decades of manufacturing best practices while providing the flexibility to accommodate unique organizational requirements. The system supports multiple planning strategies including make-to-stock, make-to-order, assemble-to-order, and engineer-to-order scenarios within a single integrated framework.
Multi-level bill of materials processing can handle complex product structures including phantom assemblies, co-products, and by-products. The system automatically calculates net requirements considering on-hand inventory, scheduled receipts, and safety stock policies while accommodating lot sizing rules and supplier minimum order quantities.
Supplier collaboration capabilities enable real-time sharing of demand forecasts and production schedules with key suppliers. Electronic data interchange and web-based supplier portals facilitate efficient communication while maintaining data security and integrity. Advanced supplier performance metrics track delivery reliability, quality performance, and cost competitiveness to support strategic sourcing decisions.
The planning process incorporates sophisticated exception management capabilities that automatically identify potential problems and suggest corrective actions. Planners receive intelligent notifications about material shortages, capacity constraints, and delivery conflicts before they impact production schedules. The system can automatically generate purchase requisitions and production orders based on predefined approval workflows and authorization limits.
Shop Floor Control and Execution
Manufacturing execution capabilities in Infor LN bridge the gap between production planning and actual shop floor activities. The system provides real-time visibility into work-in-process inventory, equipment status, and operator productivity while maintaining the flexibility to accommodate dynamic production requirements.
Work order management encompasses the complete production lifecycle from initial release through final completion and cost closure. The system supports complex routing structures including parallel operations, alternative sequences, and conditional logic based on product characteristics or customer specifications. Real-time data collection capabilities track actual labor hours, material consumption, and quality measurements against planned values.
Resource scheduling algorithms optimize the assignment of personnel and equipment to production activities based on skills requirements, availability, and efficiency considerations. The system can automatically reschedule activities to accommodate unplanned equipment downtime or operator absences while maintaining delivery commitments.
Quality integration ensures that quality control checkpoints are embedded throughout the production process rather than relegated to final inspection activities. Statistical process control capabilities monitor key quality parameters in real-time and trigger automatic adjustments when measurements drift outside acceptable ranges.
Working with experienced Infor LN consultants ensures that shop floor control capabilities are configured and optimized to match specific organizational requirements and production methodologies.
Advanced Features Transforming Manufacturing Operations
Intelligent Demand Sensing and Forecasting
Traditional demand forecasting relies heavily on historical sales data and simple statistical models that often fail to capture the complexity and volatility of modern markets. Infor LN incorporates advanced demand sensing capabilities that process multiple data streams simultaneously to generate more accurate and responsive demand predictions.
The system analyzes point-of-sale data, inventory levels, promotional activities, weather patterns, economic indicators, and social media sentiment to identify demand signals that traditional forecasting methods might miss. Machine learning algorithms automatically adjust forecasting models based on prediction accuracy and changing market conditions.
Collaborative demand planning capabilities enable sales teams, marketing organizations, and key customers to contribute demand intelligence that enhances forecast accuracy. The system provides role-based dashboards that allow different stakeholders to contribute their unique perspectives while maintaining data integrity and version control.
Scenario planning tools enable manufacturers to evaluate the impact of different demand assumptions on production capacity, inventory levels, and financial performance. These capabilities are particularly valuable for new product introductions, market expansion initiatives, and capacity investment decisions.
Predictive Maintenance and Asset Optimization
Equipment downtime represents one of the most significant cost drivers in manufacturing operations. According to ITIC, 86% of manufacturing firms state that a single hour of downtime in their systems, networks, applications or other hardware can cost at least $300,000. This statistic underscores the critical importance of effective maintenance strategies and asset management practices.
Infor LN incorporates comprehensive asset management capabilities that extend far beyond traditional preventive maintenance scheduling. The platform integrates with industrial IoT sensors and monitoring systems to collect real-time equipment performance data including vibration patterns, temperature measurements, pressure readings, and energy consumption metrics.
Advanced analytics algorithms analyze this data stream to identify patterns that indicate impending equipment failures. These predictive models consider equipment age, operating conditions, maintenance history, and environmental factors to generate failure probability assessments and recommended maintenance actions. The system automatically schedules maintenance activities based on these predictions while considering production schedules and resource availability.
Maintenance planning capabilities optimize the allocation of skilled technicians, spare parts, and specialized tools across multiple maintenance activities. The system can automatically reschedule maintenance tasks to minimize production impact while ensuring that critical equipment reliability requirements are maintained.
Integration with Infor EAM provides additional asset management capabilities for organizations with complex maintenance requirements and extensive equipment inventories.
Advanced Quality Management Systems
Quality management in modern manufacturing extends far beyond traditional inspection and testing activities. Contemporary quality systems must address regulatory compliance, customer requirements, supplier performance, and continuous improvement initiatives within an integrated framework that supports both prevention and detection strategies.
Infor LN provides comprehensive quality management capabilities that integrate with production processes to ensure that quality control activities are embedded throughout the manufacturing lifecycle rather than added as afterthoughts. The system supports multiple quality methodologies including Six Sigma, Lean Manufacturing, and Total Quality Management principles.
Statistical Process Control capabilities monitor key quality parameters in real-time and automatically trigger corrective actions when measurements indicate process drift or quality degradation. Control charts and capability studies provide visual feedback to operators and quality personnel while maintaining comprehensive documentation for regulatory compliance and continuous improvement initiatives.
Supplier quality management extends quality control activities beyond internal operations to encompass the entire supply chain. The system tracks supplier quality performance, manages corrective action requests, and maintains supplier certifications and audits. Incoming inspection workflows ensure that purchased materials meet quality requirements before entering production processes.
Customer complaint management workflows track quality issues from initial detection through root cause analysis and corrective action implementation. The system automatically generates quality alerts when similar problems are detected in other products or production lots, enabling proactive quality management rather than reactive problem-solving.
Cost Management and Profitability Analysis
Understanding true product costs and profitability represents a fundamental requirement for manufacturing success, yet many traditional costing systems provide incomplete or misleading information that can lead to poor strategic decisions. Infor LN incorporates sophisticated costing methodologies that provide accurate, actionable insights into product profitability and operational efficiency.
Activity-Based Costing capabilities allocate overhead expenses based on actual resource consumption rather than simple volume-based allocation methods. This approach provides more accurate product costs by recognizing that different products consume support services at different rates. The system automatically collects activity data from production operations, quality control processes, and support functions to ensure that cost allocations reflect actual resource utilization.
Standard costing functionality maintains detailed cost standards for materials, labor, and overhead components while providing comprehensive variance analysis that identifies the sources of cost differences. The system can automatically adjust standard costs based on actual performance data or maintain static standards for budgeting and performance measurement purposes.
Profitability analysis extends beyond simple margin calculations to consider customer-specific costs, channel expenses, and lifecycle profitability patterns. The system can analyze profitability by product, customer, sales territory, or any other relevant dimension to support strategic decision-making and resource allocation.
Project costing capabilities track costs and profitability for complex, long-duration manufacturing projects including engineer-to-order products and custom manufacturing services. The system provides real-time project status information and automated alerts when projects exceed budget thresholds or timeline commitments.
Ready to revolutionize your manufacturing operations with Infor LN?
Sama specializes in Infor LN implementation and optimization for manufacturing companies, helping you leverage advanced ERP features to streamline production, improve efficiency, and accelerate digital transformation in your manufacturing processes.
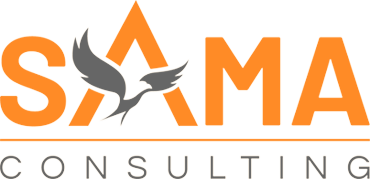
Industry 4.0 Integration and Smart Manufacturing
IoT Integration and Sensor Data Processing
The Internet of Things revolution is transforming manufacturing operations by providing unprecedented visibility into equipment performance, environmental conditions, and process parameters. Infor LN incorporates comprehensive IoT integration capabilities through Infor ION that enable manufacturers to leverage sensor data for operational optimization and predictive analytics.
The platform can process data streams from thousands of sensors simultaneously, analyzing temperature, pressure, vibration, energy consumption, and other critical parameters in real-time. Advanced analytics algorithms identify patterns and anomalies that indicate equipment problems, process variations, or quality issues before they impact production operations.
Edge computing capabilities enable local data processing and decision-making at the production facility level while maintaining connectivity to centralized systems for coordination and reporting. This approach reduces network bandwidth requirements and improves system responsiveness for time-critical applications.
Machine learning algorithms continuously analyze sensor data to improve predictive models and optimize process parameters. The system can automatically adjust machine settings based on material characteristics, environmental conditions, or quality requirements while maintaining operator oversight and approval capabilities.
Digital twin technology creates virtual representations of physical equipment and processes that enable simulation and optimization before implementing changes in actual production environments. These virtual models incorporate real-time sensor data to maintain accuracy while supporting what-if analysis and optimization studies.
Artificial Intelligence and Machine Learning Applications
Artificial intelligence and machine learning technologies are transforming manufacturing operations by automating complex decision-making processes and identifying optimization opportunities that human analysts might overlook. Infor LN incorporates AI capabilities throughout the manufacturing process to enhance efficiency, quality, and responsiveness.
Demand forecasting algorithms analyze multiple data sources including sales history, market trends, weather patterns, and economic indicators to generate more accurate demand predictions. These models automatically adjust their parameters based on forecast accuracy and changing market conditions, continuously improving their performance over time.
Production scheduling optimization employs AI algorithms to evaluate millions of potential schedule combinations and select solutions that optimize multiple objectives simultaneously. The system considers material availability, capacity constraints, setup times, and delivery requirements to generate feasible schedules that maximize operational efficiency.
Quality prediction models analyze production process data to identify conditions that are likely to result in quality problems. These models can recommend process adjustments or trigger additional quality control measures before defective products are produced, reducing waste and improving customer satisfaction.
Supply chain optimization algorithms analyze supplier performance, market conditions, and risk factors to recommend sourcing strategies and inventory levels that balance cost, service, and risk considerations. The system can automatically adjust safety stock levels and reorder points based on demand variability and supplier reliability.
Digital Twin Technology and Simulation
Digital twin technology represents one of the most promising applications of Industry 4.0 concepts in manufacturing environments. By creating virtual representations of physical assets, processes, and systems, manufacturers can simulate different scenarios, optimize operations, and predict future performance without disrupting actual production activities.
Infor LN supports digital twin implementations through comprehensive data integration capabilities that connect virtual models with real-time operational data. These digital twins incorporate equipment specifications, process parameters, material properties, and environmental conditions to create accurate representations of actual manufacturing operations.
Process simulation capabilities enable manufacturers to evaluate the impact of process changes, equipment modifications, or capacity expansions before implementing them in actual production environments. These simulations consider complex interactions between different process steps, resource constraints, and quality requirements to provide realistic assessments of proposed changes.
Equipment digital twins monitor actual equipment performance against designed specifications and operating parameters. These models can predict maintenance requirements, identify optimization opportunities, and simulate the impact of different operating strategies on equipment life and performance.
Factory-level digital twins integrate individual equipment and process models into comprehensive facility simulations that support strategic planning and operational optimization. These models can evaluate the impact of product mix changes, capacity modifications, or layout reconfigurations on overall facility performance.
Ready to revolutionize your manufacturing operations with Infor LN?
Sama specializes in Infor LN implementation and optimization for manufacturing companies, helping you leverage advanced ERP features to streamline production, improve efficiency, and accelerate digital transformation in your manufacturing processes.
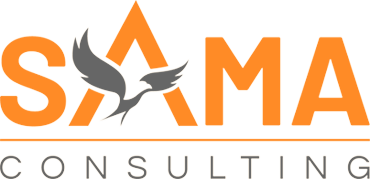
Supply Chain Excellence Through Intelligent Orchestration
End-to-End Supply Chain Visibility
Modern manufacturing operations depend on complex, multi-tier supply networks that span multiple countries, currencies, and regulatory environments. Traditional supply chain management approaches that focus on immediate suppliers and customers are insufficient for managing these complex relationships effectively. Infor LN provides comprehensive supply chain visibility capabilities that extend across the entire value network.
The platform integrates with supplier systems, logistics providers, and customer platforms to provide real-time visibility into material flows, inventory positions, and delivery status throughout the supply chain. Advanced tracking capabilities monitor shipments from initial dispatch through final delivery while providing automated notifications of delays, damages, or other exceptions.
Supply chain mapping capabilities identify all participants in complex supply networks including sub-tier suppliers, contract manufacturers, and logistics providers. This visibility enables better risk assessment and mitigation strategies while supporting compliance with regulations that require supply chain transparency.
Demand collaboration tools enable real-time sharing of demand forecasts and production schedules with key suppliers and customers. This collaboration reduces bullwhip effects and enables more efficient inventory management across the entire supply chain.
For organizations requiring comprehensive supply chain capabilities, Infor supply chain management solutions provide additional functionality and specialized tools for complex supply chain scenarios.
Supplier Relationship Management
Effective supplier relationship management extends far beyond traditional procurement activities to encompass strategic partnership development, performance monitoring, and risk management. Infor LN provides comprehensive supplier management capabilities that support both tactical procurement operations and strategic supplier development initiatives.
Supplier qualification and certification workflows ensure that potential suppliers meet quality, financial, and operational requirements before being approved for specific products or services. The system maintains comprehensive supplier profiles including certifications, capabilities, capacity information, and performance history.
Performance monitoring capabilities track supplier delivery reliability, quality performance, cost competitiveness, and service responsiveness using configurable scorecards and dashboards. Automated alerts notify procurement teams when supplier performance falls below acceptable thresholds, enabling proactive intervention before problems impact production operations.
Supplier development programs support collaborative improvement initiatives that enhance supplier capabilities and performance. The system tracks improvement projects, measures results, and maintains documentation for certification and audit purposes.
Risk management tools assess supplier financial stability, geographic concentration, and operational risks to identify potential supply disruptions before they occur. The system can automatically recommend alternative sourcing strategies or inventory adjustments when risk levels exceed acceptable thresholds.
Advanced Logistics and Distribution
Logistics and distribution operations represent critical links between manufacturing facilities and customers, yet they are often overlooked in traditional ERP implementations. Infor LN provides comprehensive logistics management capabilities that optimize transportation costs, delivery performance, and customer service levels.
Transportation planning algorithms consider multiple factors including shipment consolidation opportunities, carrier capabilities, routing efficiency, and delivery requirements to select optimal shipping strategies. The system can automatically generate shipping documents, track shipments, and provide delivery notifications to customers.
Warehouse management integration provides real-time visibility into inventory positions, picking operations, and shipping activities. Advanced allocation algorithms optimize inventory placement and picking sequences to minimize handling costs and delivery times.
Load planning capabilities optimize truck loading to maximize capacity utilization while considering weight restrictions, dimensional constraints, and delivery sequence requirements. The system can automatically generate loading instructions and documentation to ensure efficient warehouse operations.
For organizations with complex warehouse operations, comprehensive warehouse management solutions provide additional functionality including advanced inventory optimization and automation capabilities.
Quality Management and Regulatory Compliance
Comprehensive Quality Control Systems
Quality management in modern manufacturing requires sophisticated systems that integrate with production processes to prevent quality problems rather than simply detect them after they occur. Infor LN provides comprehensive quality management capabilities that embed quality control activities throughout the manufacturing lifecycle.
Incoming inspection workflows ensure that purchased materials meet quality specifications before entering production processes. The system supports various inspection methodologies including sampling plans, attribute testing, and variable measurement techniques. Automated acceptance and rejection procedures ensure consistent quality decisions while maintaining comprehensive documentation for regulatory compliance.
In-process quality control capabilities monitor key quality parameters during production operations and automatically trigger corrective actions when measurements indicate process drift or quality degradation. Statistical Process Control charts provide real-time feedback to operators while maintaining historical data for trend analysis and process improvement initiatives.
Final inspection and testing workflows ensure that finished products meet all quality requirements before shipment to customers. The system supports complex testing protocols including environmental testing, performance validation, and regulatory compliance verification. Automated test equipment integration eliminates manual data entry while ensuring data accuracy and integrity.
Quality documentation management maintains comprehensive quality records including test results, certifications, and audit trails. The system can automatically generate quality certificates, compliance reports, and regulatory submissions while ensuring that all documentation meets industry and regulatory requirements.
Regulatory Compliance and Audit Trails
Manufacturing organizations operate in increasingly complex regulatory environments that require comprehensive documentation, traceability, and reporting capabilities. Infor LN provides sophisticated compliance management tools that address FDA validation, ISO certification, and industry-specific regulatory requirements.
Validation support capabilities address the unique requirements of regulated industries including pharmaceutical, medical device, and food manufacturing. The system maintains comprehensive documentation of validation activities, change control procedures, and ongoing compliance monitoring. Electronic signatures and audit trails ensure that all system changes are properly authorized and documented.
Traceability capabilities track materials and products throughout the manufacturing process from raw material receipt through final product shipment. The system can automatically generate genealogy reports that identify all materials, processes, and personnel involved in manufacturing specific products or production lots.
Change control workflows ensure that all product, process, and system changes are properly evaluated, approved, and documented before implementation. The system maintains comprehensive change histories and can automatically assess the impact of proposed changes on existing products and processes.
Regulatory reporting capabilities automatically generate required reports and submissions for various regulatory agencies. The system maintains current regulatory requirements and can alert users when new regulations or reporting requirements are implemented.
Financial Impact and Return on Investment
Quantifying Manufacturing ERP Benefits
ERP systems save manufacturers 22% in operational costs, representing significant financial benefits that extend across multiple operational dimensions. However, understanding the complete financial impact of Infor LN implementations requires analysis of both direct cost savings and indirect benefits that may be more difficult to quantify but equally important for long-term success.
Direct cost savings typically manifest in several key areas. Inventory reduction represents one of the most significant sources of cost savings, with organizations frequently achieving 15-25% reductions in inventory carrying costs through improved demand forecasting, better supplier collaboration, and optimized safety stock policies. These reductions free up working capital that can be reinvested in growth initiatives or returned to shareholders.
Labor productivity improvements result from automation of manual processes, elimination of data entry errors, and more efficient workflow management. Organizations typically report 10-20% improvements in administrative productivity and 5-15% improvements in direct labor efficiency through better production scheduling and resource allocation.
Material cost savings emerge from improved supplier negotiation capabilities, reduced expediting costs, and better supplier performance management. Organizations frequently achieve 3-7% reductions in material costs through strategic sourcing initiatives and improved supplier collaboration.
Operational Excellence Metrics
ERP systems can reduce the time to make business decisions by 36%, highlighting the significant impact of improved information availability and analytical capabilities on organizational agility and responsiveness. This improvement in decision-making speed translates into competitive advantages that may be difficult to quantify but are critically important for long-term success.
On-time delivery performance typically improves by 15-30% through better production planning, improved supplier collaboration, and enhanced visibility into production status and potential delays. These improvements enhance customer satisfaction and reduce the costs associated with expediting, premium freight, and customer complaints.
Ready to revolutionize your manufacturing operations with Infor LN?
Sama specializes in Infor LN implementation and optimization for manufacturing companies, helping you leverage advanced ERP features to streamline production, improve efficiency, and accelerate digital transformation in your manufacturing processes.
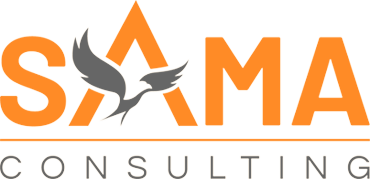
Conclusion
Infor LN stands as a transformative force in the manufacturing industry, redefining operational excellence through its advanced ERP capabilities. By addressing the complexities of modern manufacturing—such as volatile supply chains, evolving customer demands, and stringent regulatory requirements—Infor LN empowers organizations to transition from reactive to proactive, data-driven operations. Its robust architecture, seamlessly integrating cutting-edge technologies like AI, IoT, and digital twins, enables manufacturers to optimize production, enhance quality, and achieve end-to-end supply chain visibility. The platform’s scalability, multi-site support, and industry-specific features ensure it meets the diverse needs of global enterprises while driving measurable financial benefits, including significant cost reductions and improved decision-making agility.
Author Bio
Rajen Goswami is a technical consultant specializing in Infor ION, Infor LN, and Baan systems. He designs and implements robust integrations and customizations, enabling seamless data flows, process automation, and functional enhancements across enterprise environments.