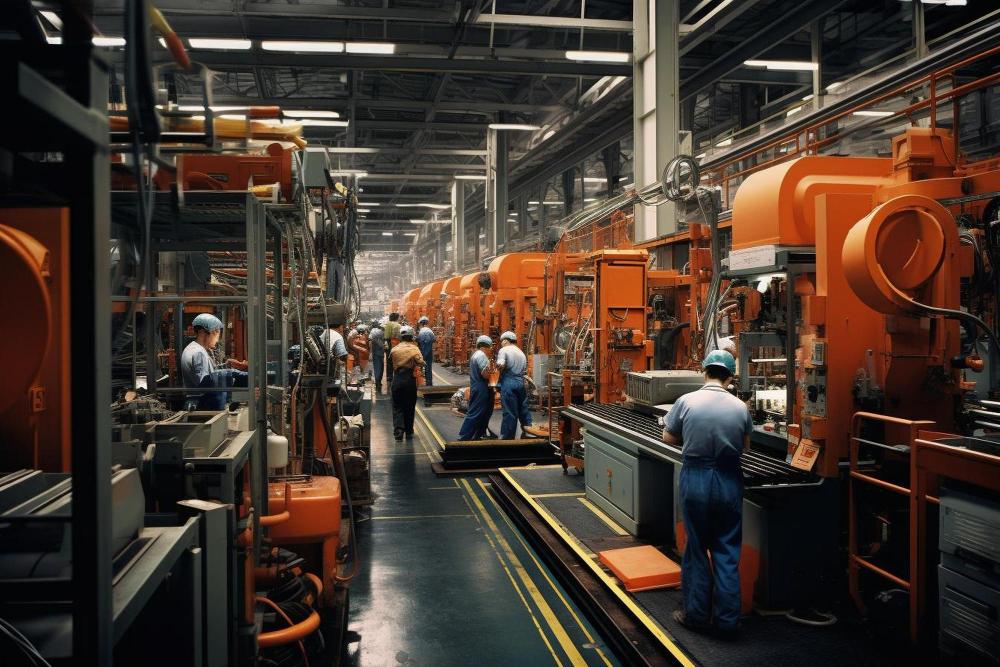
MES vs ERP: Exploring the Key Differences
Introduction
Understanding the major differences between an MES and ERP system is crucial for anyone in the manufacturing industry. Both systems play pivotal roles yet cater to different aspects of production and business operations.
MES (Manufacturing Execution System) focuses on tracking and monitoring raw materials and goods throughout the production process. It captures real-time data, enabling manufacturers to optimize production efforts, enforce process requirements, and improve product quality.
On the other hand, ERP (Enterprise Resource Planning) systems manage a wide range of operational activities. They integrate various business processes with manufacturing processes, providing comprehensive reports on business operations, scheduling plant functions, and ensuring better inventory control.
Knowing these distinctions helps manufacturers:
- Enhance operational efficiency
- Reduce costs
- Improve overall productivity
The proper integration of both systems can significantly impact a company’s bottom line by offering real-time visibility and detailed historical analysis. For instance, in the automotive industry, this integration can streamline processes across the supply chain from “automotive manufacturers to dealerships”. Similarly, in the distribution sector, it can optimize inventory management and logistics from “warehouses to retailers”, leading to improved profitability.
What is an MES?
An MES (Manufacturing Execution System) is a software solution designed to monitor and manage manufacturing operations on the factory floor. The primary purpose of an MES is to ensure efficient execution of manufacturing processes by capturing and analyzing real-time data throughout the production process.
Definition and Purpose
An MES operates as a bridge between enterprise-level planning systems, such as ERP, and the control systems on the manufacturing floor. It collects real-time data from machines and operators, providing a comprehensive view of production activities. This enables manufacturers to:
- Track and document the transformation of raw materials into finished goods.
- Enforce process control and compliance with production standards.
- Optimize resource usage and enhance overall operational efficiency.
Real-Time Data Capture
One of the key strengths of an MES is its ability to capture real-time data during production. This data includes information such as:
- Machine performance metrics
- Operator activity logs
- Material consumption rates
- Production output levels
By collecting this information in real-time, an MES allows for immediate detection of issues, such as equipment malfunctions or deviations from quality standards. This leads to quicker responses and minimizes downtime.
Impact on Product Quality
Monitoring and optimization through an MES have a significant impact on product quality. Continuous tracking ensures that every step in the production process adheres to predefined specifications. Analyzing real-time data provides insights into potential areas for improvement, leading to:
- Enhanced product consistency
- Reduced waste and rework
- Increased customer satisfaction.
To further enhance manufacturing processes, it is crucial for businesses to embrace cloud technology. Cloud-based MES solutions offer numerous benefits such as scalability, flexibility, and cost-effectiveness. By tailoring your cloud strategy to meet specific business needs rather than adopting a one-size-fits-all approach, you can maximize the value derived from the technology and ensure a successful transition.”.
What is an ERP System?
Enterprise Resource Planning (ERP) systems are comprehensive software solutions designed to manage and streamline various business processes across an organization. The primary purpose of an ERP system is to facilitate the flow of information between all business functions, ensuring efficient management of resources and operations.
Definition and Purpose
An ERP system integrates multiple facets of a business, including:
- Finance
- Human Resources
- Supply Chain Management
- Customer Relationship Management
By consolidating data from these diverse departments into a single unified system, ERPs provide a holistic view of the organization’s performance. This integration enhances decision-making capabilities through real-time data access and analysis.
Managing Financial Transactions and Granular Data
A significant advantage of ERP systems lies in their ability to manage financial transactions and granular data across various departments. Key functionalities include:
- Automated financial reporting: Streamlining accounting processes such as accounts payable, accounts receivable, and general ledger management.
- Inventory control: Monitoring stock levels, order fulfillment, and procurement processes.
- Resource planning: Scheduling tasks, allocating resources efficiently, and tracking project progress.
ERPs not only automate repetitive tasks but also ensure compliance with industry standards and regulations. This automation reduces human error and enhances operational efficiency.
In industries like construction and engineering, ERP systems play a crucial role in project visibility, resource optimization, quality assessments, and supply chain simplification. For example, they can help optimize execution and resources by providing project visibility. Additionally, ERPs offer automated QA assessments for improved quality control. Moreover, they simplify the supply chain by streamlining processes. Lastly, they allow for engineer-to-order functionality which optimizes delivery in sectors such as construction and engineering.
Learn more about these applications here.
Functionality Comparison: MES vs ERP Systems
MES and ERP systems serve distinct functions within a manufacturing environment. Understanding these differences is crucial for optimizing shop floor operations and business processes.
Key Functional Differences
- MES focuses on real-time operations in the manufacturing process. It captures and monitors data directly from the shop floor, providing immediate insights into production activities. This real-time data helps in monitoring and optimizing product quality, reducing operation costs, and improving productivity.
- ERP systems are more about planning and analysis. They handle scheduling of plant functions, manage financial transactions, and integrate various business processes with manufacturing operations. The ERP system provides a broader view of the organization’s performance through historical data analysis rather than immediate operational details.
Real-Time Operations vs Planning and Analysis
Real-time operations are where MES truly excels. By integrating directly with machines on the factory floor, it ensures that production data is continuously updated. This immediate feedback loop is vital for making quick adjustments to maintain efficiency and product quality.
On the other hand, planning and analysis are the domain of ERP systems. With a focus on long-term strategic goals, ERP systems analyze historical data to inform decisions on inventory control, customer relationship management, and overall business growth strategies.
For manufacturers looking to optimize both their shop floor operations and strategic planning efforts, understanding these core functionalities can help in selecting the right system or combination of systems for their needs.
To further enhance shop floor operations, businesses can also explore supply chain optimization. This approach streamlines operations, reduces costs, and enhances agility for sustained success. Additionally, for heavy equipment manufacturers specifically, there are tailored solutions available that can optimize sales, leading to extra efficiency and improved customer satisfaction. These solutions encompass everything from accurate pricing guidance to predictive maintenance, empowering equipment businesses to achieve their goals and build stronger relationships with customers.
Need help with your ERP evaluation process?
We will provide a detailed, unbiased evaluation by assessing your business needs, shortlisting vendors, analyzing cost benefits, planning implementation, and mitigating risks.
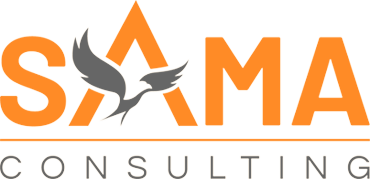
Reporting Capabilities: Real-Time vs General Reports
MES excels in providing real-time data capture, allowing manufacturers to gain instant insights into their production processes. This capability ensures that any deviations or issues are immediately identified and addressed. For instance, if a machine on the factory floor starts showing signs of malfunction, the MES can alert operators instantly, minimizing downtime and potential losses.
ERP systems, on the other hand, focus on generating historical overviews and comprehensive reports. These reports are crucial for long-term planning and strategic decision-making. By examining trends over time, ERP systems enable businesses to forecast demand, manage inventory efficiently, and optimize resource allocation.
Key Differences in Reporting Capabilities:
Immediate Insights (MES):
- Real-time visibility into production.
- Instant alerts for anomalies.
- Enhanced ability to make quick decisions.
Historical Overviews (ERP):
- Detailed analysis of past performance.
- Long-term trend identification.
- Strategic planning based on extensive data.
Integrating MES with ERP allows manufacturers to leverage the strengths of both systems, ensuring seamless data flow from real-time operations to long-term planning. This integration enhances overall operational efficiency by combining immediate responsiveness with strategic foresight.
For more information on optimizing logistics and integrating business processes, explore how Logistics Service Providers can play a vital role in this endeavor.
By understanding these distinctions, you can better tailor your approach to manufacturing management, ensuring both immediate efficiency and long-term success.
System Integration: MES and ERP
System integration between MES and ERP systems involves several approaches, each designed to enhance data flow and operational efficiency. One common method is integrating MES directly with machines on the factory floor, enabling real-time data capture. This data is then transmitted to the ERP system, typically via a shared database or HTTP communication, providing a comprehensive overview of manufacturing operations.
Benefits of Integrating MES and ERP Systems
- Enhanced Data Flow: Seamless integration ensures continuous data exchange between shop-floor activities and business processes.
- Operational Insight: Real-time updates from MES enrich ERP’s planning and analysis capabilities, supporting better decision-making.
- Improved Efficiency: Automation of data transfer reduces manual entry errors, streamlining workflows across departments.
- Comprehensive Reporting: Combining real-time production data with historical business data offers a holistic view of operational performance.
Need help with your ERP evaluation process?
We will provide a detailed, unbiased evaluation by assessing your business needs, shortlisting vendors, analyzing cost benefits, planning implementation, and mitigating risks.
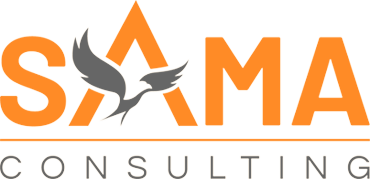
Challenges of Integrating MES and ERP Systems
- Complexity: The integration process can be technically challenging, requiring specialized knowledge and resources.
- Cost: Initial setup and ongoing maintenance may involve significant investment.
- User Adoption: Diverse user bases need to adapt to new integrated systems, which may entail training and change management efforts.
By addressing these challenges thoughtfully, manufacturers can leverage the synergy between MES and ERP systems to optimize plant efficiency.
Customization and Flexibility
When evaluating customization and flexibility in MES and ERP systems, it’s essential to understand their distinct approaches.
MES Systems
MES systems are primarily tailored for shop-floor activities. They can be customized to fit specific manufacturing processes and allow real-time adjustments to production workflows. MES also offers modules that can be added or removed based on unique production requirements.
Example: A car manufacturing plant might need an MES that tracks the assembly line in minute detail. The system can be configured to monitor each stage of the workflow, ensuring quality control at every step.
ERP Systems
On the other hand, ERP systems are designed for broader organizational needs. Customization often involves integrating various business functions, and they focus on adapting to different departmental workflows such as finance, HR, and inventory management. Although flexible, significant changes might require extensive reconfiguration and testing.
Example: An ERP system used by a large retail chain may integrate financial management with supply chain logistics. Customizing this system involves aligning it with multiple departments’ requirements, ensuring seamless data flow across the organization.
Both systems offer flexibility, but the scope and nature of customization differ significantly. MES provides immediate adaptability for production processes, while ERP delivers broader integration across business functions.
Conclusion
Understanding the comparison of MES and ERP systems is crucial for manufacturers aiming to optimize their operations. Both systems play distinct, yet complementary roles in manufacturing processes.
MES focuses on real-time monitoring and control of the shop-floor activities. By capturing data directly from production equipment, it ensures high product quality and operational efficiency. Real-time visibility into production processes allows for immediate adjustments, reducing downtime and waste.
ERP systems handle broader organizational needs, integrating business processes with manufacturing workflows. They manage financial transactions, inventory levels, customer orders, and compliance requirements. ERP systems provide historical data analysis and help in strategic planning by offering comprehensive reports across departments.
Each system brings unique benefits:
MES:
- Real-time data capture
- Process enforcement
- Enhanced product quality
ERP:
- Integrated business processes
- Improved inventory control
- Automation for risk mitigation
Integration of MES and ERP systems ensures seamless data flow from the factory floor to executive decision-makers. This integration maximizes plant efficiency by providing a holistic view of manufacturing operations.
Manufacturers must leverage both MES and ERP systems to achieve optimal performance and maintain a competitive edge in the industry.
Need help with your ERP evaluation process?
We will provide a detailed, unbiased evaluation by assessing your business needs, shortlisting vendors, analyzing cost benefits, planning implementation, and mitigating risks.
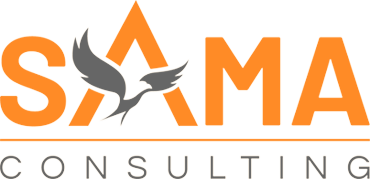