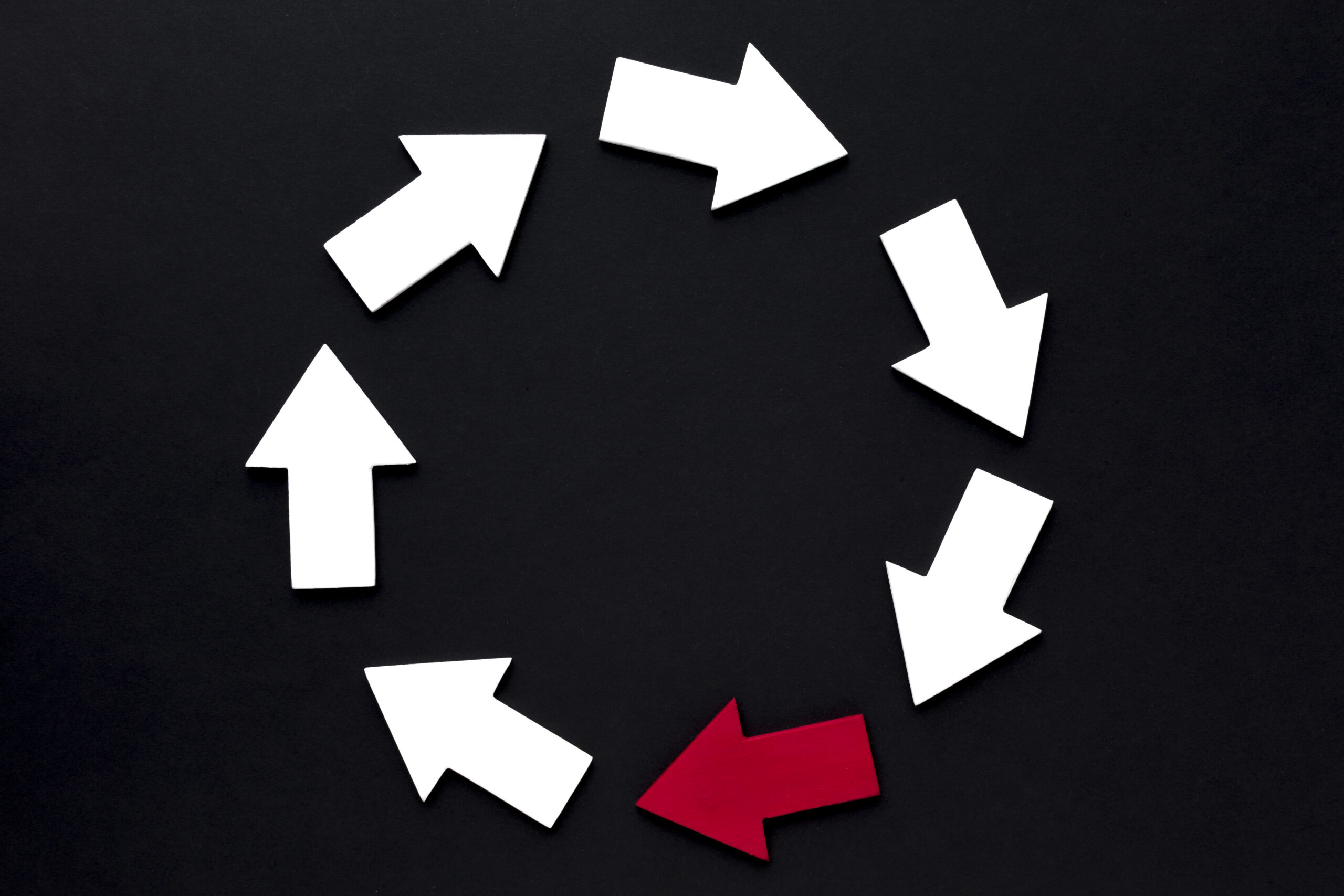
Mastering Product Lifecycle Management: Unlocking Efficiency and Innovation in Modern Businesses
In an era where innovation cycles are shrinking and customer expectations are soaring, Product Lifecycle Management (PLM) has emerged as a linchpin for businesses striving to stay competitive. Far more than a software suite, PLM is a strategic framework that governs a product’s journey from inception to obsolescence, harmonizing people, processes, and technology. Whether you operate in automotive, aerospace and defense, or high-tech electronics, PLM can revolutionize how you design, produce, and sustain your products. This in-depth guide explores the technical nuances of PLM, its stages, tools, benefits, and real-world applications, offering a roadmap to harness its full potential—all crafted with expertise, authority, and trustworthiness in mind.
What is Product Lifecycle Management (PLM)?
Product Lifecycle Management is a holistic discipline that oversees a product’s entire existence—from the flicker of an idea to its final disposal. It’s a blend of strategy and technology designed to centralize product data, streamline workflows, and foster collaboration across departments. At its heart, PLM ensures that every stakeholder—from engineers to supply chain managers—works from a unified, accurate dataset, eliminating guesswork and redundancies.
For industries like industrial manufacturing or heavy equipment, where precision is critical, PLM acts as a digital backbone, managing complex designs, regulatory compliance, and production schedules. It’s not just about tracking a product; it’s about optimizing its lifecycle to maximize value, reduce waste, and accelerate delivery.
Key Objectives of PLM
- Centralized Data Management: Consolidates all product-related information—CAD files, Bills of Materials (BOMs), specifications—into a single, accessible repository.
- Process Optimization: Identifies bottlenecks and automates repetitive tasks, boosting efficiency.
- Collaboration: Bridges gaps between design, manufacturing, and marketing teams for real-time alignment.
- Compliance: Ensures products meet industry standards, such as ISO 9001 or FDA regulations.
- Innovation: Facilitates rapid prototyping and iterative design, keeping businesses ahead of market trends.
PLM’s versatility makes it indispensable across sectors, from construction engineering to logistics service providers.
Ready to revolutionize your product lifecycle management?
Sama delivers expert PLM implementations, streamlining your product development from concept to end-of-life while enhancing collaboration, reducing time-to-market, and ensuring regulatory compliance.
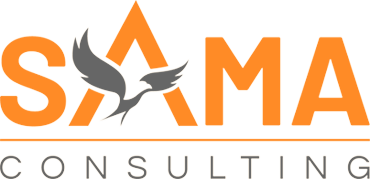
The SILO: Breaking Down PLM
To deliver a comprehensive yet digestible exploration, we’ll use a SILO structure, organizing PLM into logical, detailed sections.
1. The Stages of the Product Lifecycle
Every product follows a lifecycle with distinct phases, each demanding specific tools and strategies. PLM provides the framework to navigate these stages seamlessly.
a. Ideation and Concept Development
The lifecycle begins with ideation—a phase where creativity meets feasibility. Teams brainstorm product ideas, analyze market trends, and define customer requirements. PLM systems capture these inputs, storing them in a digital repository linked to market research data, competitor analyses, and preliminary sketches. Tools like requirements management software (e.g., IBM DOORS) integrate with PLM to align customer needs with technical specifications.
For example, a company developing a new electric vehicle (EV) might use PLM to document range expectations, battery preferences, and regulatory constraints, ensuring all stakeholders—from designers to compliance officers—are on the same page. This phase sets the foundation for success, reducing missteps later.
b. Design and Engineering
Next comes the design phase, where concepts transform into tangible blueprints. Engineers leverage Computer-Aided Design (CAD) tools—such as SolidWorks or AutoCAD—to create detailed 2D and 3D models, while PLM systems manage versioning, revisions, and BOMs. In automotive, this might involve designing a chassis, integrating it with electrical systems, and simulating crash tests—all tracked within PLM.
PLM ensures that every design change is propagated instantly across teams, preventing costly oversights. For instance, if a supplier updates a component’s specs, PLM reflects this in the BOM, alerting manufacturing and procurement simultaneously. Simulation tools within PLM also allow engineers to test designs virtually, minimizing physical prototypes.
c. Manufacturing and Production
With the design locked in, PLM shifts focus to production. It integrates with Manufacturing Execution Systems (MES) to oversee prototyping, tooling, and full-scale assembly. This phase involves detailed process planning—defining machining tolerances, assembly sequences, and quality checks. For heavy equipment, PLM might manage the production of a bulldozer, ensuring each weld and bolt meets specs.
Supply chain coordination is critical here. PLM tracks material procurement, supplier schedules, and inventory levels, syncing with logistics service providers to avoid delays. Advanced PLM systems even support digital manufacturing, using 3D printing or CNC machining data directly from design files.
d. Distribution and Market Launch
Once produced, the product enters distribution. PLM manages packaging designs, shipping logistics, and compliance with regional regulations (e.g., CE marking in Europe). In CPG and retail, PLM ensures a new snack product reaches shelves with proper labeling and shelf-life data intact.
This phase also involves marketing handoffs—PLM shares product specs with sales teams to craft compelling campaigns. For global launches, it tracks multi-region rollouts, ensuring consistency across markets.
e. Service and Maintenance
Post-launch, PLM supports the product in use. It manages warranty claims, spare parts inventories, and service manuals. In aerospace and defense, where a jet engine might require decades of maintenance, PLM tracks every repair, replacement, and inspection, ensuring compliance with airworthiness directives.
Customer feedback loops are also integrated, allowing field data to inform future designs. For instance, if a smartphone’s battery fails prematurely, PLM logs this for the next iteration.
f. End-of-Life and Disposal
Finally, PLM governs product retirement. It plans disassembly, recycling, or disposal, adhering to environmental regulations like the EU’s WEEE Directive. In construction engineering, PLM might guide the decommissioning of a bridge, repurposing steel while safely disposing of concrete. Sustainability is a growing focus, with PLM assessing a product’s carbon footprint across its lifecycle.
2. The Technical Backbone of PLM
PLM’s power lies in its technology stack. Let’s explore the components that make it tick.
a. PLM Software
Leading PLM platforms—Siemens Teamcenter, PTC Windchill, Dassault Systèmes ENOVIA—offer robust features:
- Version Control: Tracks every design iteration, preventing conflicts.
- Workflow Automation: Automates approvals, change orders, and notifications.
- Integration: Links with ERP (e.g., SAP), CRM, and MES systems.
For businesses seeking scalability, Infor CloudSuite enhances PLM with cloud-based deployment, ideal for distributed teams.
b. Data Management
PLM acts as a “digital thread,” weaving together:
- CAD Files: Stores 3D models, assemblies, and simulations.
- BOMs: Manages multi-level BOMs, detailing every nut, bolt, and circuit.
- Metadata: Captures supplier details, compliance certificates, and testing logs.
This centralization eliminates data silos. For example, a high-tech electronics firm can access a chipset’s specs instantly, avoiding production delays.
c. Cloud and IoT Integration
Cloud-based PLM offers real-time access, scalability, and lower upfront costs—benefits detailed in Why Embrace Cloud Technology?. Meanwhile, IoT integration connects physical products to PLM. A smart appliance might report usage data, triggering maintenance alerts or design tweaks, all managed within the system.
d. Analytics and AI
AI in PLM analyzes historical data to predict failures, optimize designs, and suggest cost-saving alternatives. Pairing PLM with Infor Birst unlocks advanced dashboards, turning raw data into actionable insights.
3. Benefits of Implementing PLM
PLM delivers measurable ROI across the board.
a. Reduced Time-to-Market
By syncing design and production, PLM slashes development timelines. In high-tech electronics, a new wearable might launch months earlier, capturing market share.
b. Cost Savings
PLM reduces rework by catching errors early. A single BOM update, shared instantly, can save thousands in scrapped parts. It also optimizes material use, cutting waste.
c. Improved Quality
Real-time collaboration and version control minimize defects. In heavy equipment, this ensures a crane’s hydraulics meet safety standards.
d. Regulatory Compliance
PLM tracks certifications and audits, critical for aerospace and defense under standards like AS9100.
e. Enhanced Collaboration
Teams work from one dataset, reducing miscommunication. A marketer can access design specs to align messaging with product features.
4. PLM in Action: Industry Applications
PLM adapts to sector-specific challenges.
a. Automotive
In automotive, PLM manages thousands of parts, supplier networks, and crash-test data, ensuring vehicles meet safety and emissions standards.
b. Aerospace and Defense
For aerospace and defense, PLM ensures traceability for every bolt, meeting MIL-STD-810 and FAA requirements.
c. Industrial Manufacturing
In industrial manufacturing, PLM optimizes factory layouts and integrates with Industry 4.0 tech.
d. High-Tech Electronics
For high-tech electronics, PLM accelerates design iterations for gadgets like IoT sensors.
5. Challenges and Solutions in PLM Adoption
Adoption isn’t seamless—here’s how to tackle common roadblocks.
a. Resistance to Change
Employees may cling to old methods. Solution: Conduct workshops, showcase ROI via pilots, and involve key stakeholders early.
b. Data Migration
Legacy systems can complicate transitions. Solution: Use phased migrations, data validation tools, and expert support.
c. Integration Complexity
Connecting PLM with ERP or MES can falter. Solution: Use middleware like Infor ION for smooth interoperability.
6. The Future of PLM
PLM is evolving rapidly:
- Digital Twins: Real-time virtual models for monitoring and optimization.
- Sustainability: Lifecycle assessments to reduce environmental impact.
- AI-Driven Insights: Predictive analytics for proactive decision-making.
Ready to revolutionize your product lifecycle management?
Sama delivers expert PLM implementations, streamlining your product development from concept to end-of-life while enhancing collaboration, reducing time-to-market, and ensuring regulatory compliance.
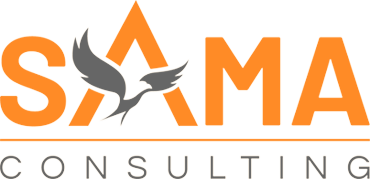
How to Get Started with PLM
- Assess Needs: Map current workflows and identify gaps.
- Choose a Platform: Select a PLM tool aligned with your industry.
- Plan Integration: Sync with existing systems.
- Train Teams: Invest in hands-on training.
- Monitor and Optimize: Use analytics to refine.
Explore tailored solutions at Sama Consulting Inc..
Conclusion
PLM is a transformative force, driving efficiency, quality, and innovation. From distribution to construction engineering, it’s a must-have for modern businesses. Start your PLM journey today—visit our blog for more insights.
Ready to revolutionize your product lifecycle management?
Sama delivers expert PLM implementations, streamlining your product development from concept to end-of-life while enhancing collaboration, reducing time-to-market, and ensuring regulatory compliance.
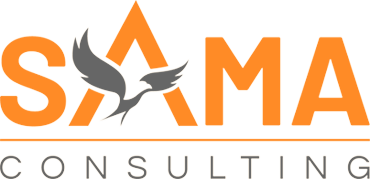